It takes an innovative approach to achieve success in the marketplace as a medium-sized compounder. AKRO-PLASTIC GmbH from Niederzissen, in Germany’s Rheinland-Pfalz, knows this first hand. But such an approach requires across-the-board coordination in all areas. Together with machine builder and sister company FEDDEM GmbH & Co. KG, AKRO‑PLASTIC has developed an integrated concept for flexible compounding.
“Stricter requirements regarding order lead times, consistent quality in manufactured products, greater product variety, and of course, global availability at competitiveprices: these are the hallmarks of our business environment”, says Thilo Stier, Head of Sales and Innovation at AKRO-PLASTIC. “Our goal is to guarantee satisfied customers and our competitive capacity without fail”.
Ensuring the required flexibility
According to the compounder, the most important building block for a flexible production process in the approach he calls ICX® (Innovative Compounding and Extrusion) technology is a standardised line concept (see Figure 1). The FED 26 MTS to FED 82 MTS line from FEDDEM is a standardised machine fleet available in 6 different sizes, optimally designed to cover applications ranging incrementally from 10 to 100 kg/h all the way to 1 500 to 3 500 kg/h, depending on the machine size. Thanks to the closely spaced increments, a FED 72 MTS can operate not only in the optimal range between 600 and 2 000 kg/h, but also in the range of the smaller model series, between 250 and 800 kg/h. The identical design makes for easy scaling up or down to support this capability of flexible line utilisation. In addition to a uniform extruder design, uniform design of the peripheral equipment is an absolute must for ensuring systematic implementation of the standardised line concept and making optimal use of the effects described; this starts with material conveyance, includes the dosing units and pelletisers with a sorting screen, and ends with filling units (see Figure 2). Flexible utilisation of this type allows for high availability in production capacity in the sense that the machine size and corresponding throughput can be modified as needed to suit the product quantity. This ensures high efficiency of the installed production capacity.
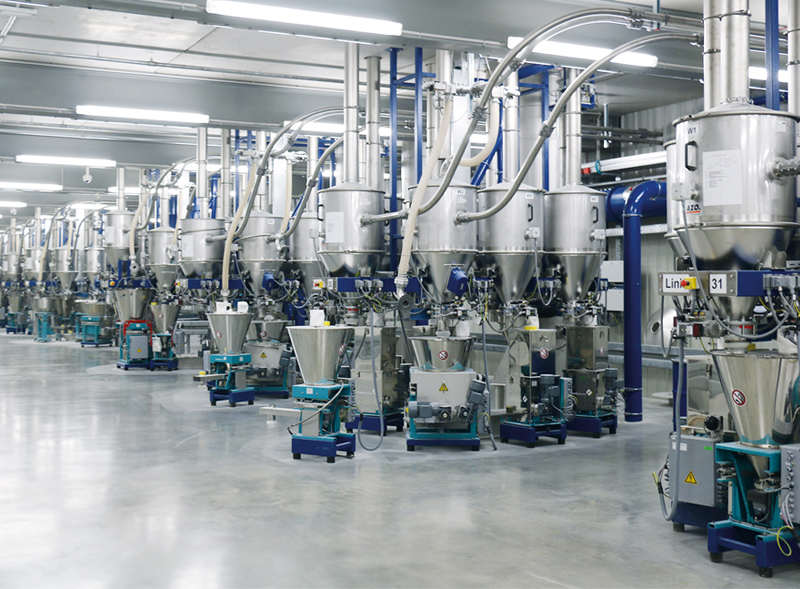
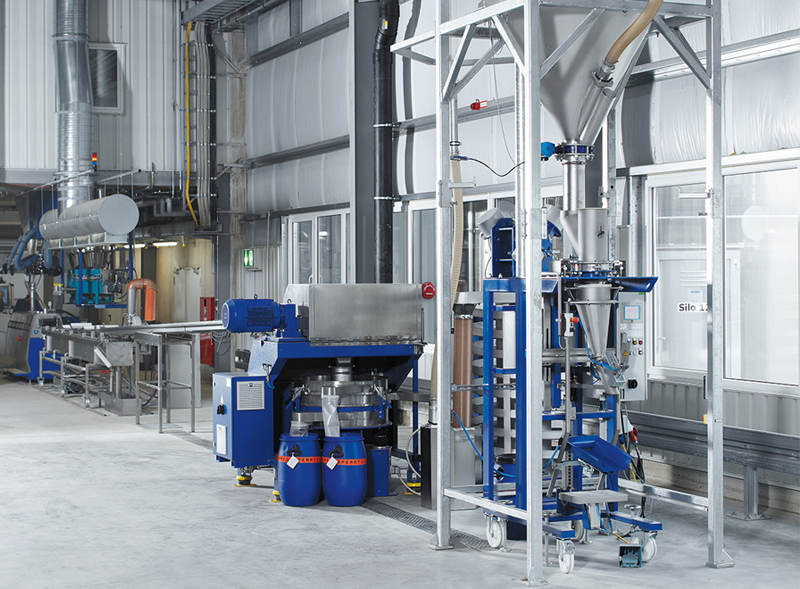
Set-up time drives efficiency
When small batches are produced, the ratio of set-up time to productive operating time of the machine increases disproportionately. “The manifold possibilities of our machine fleet allow us to operate in the optimal extruder application range at all times”, says Marc Tenne, Head of Production at AKRO-PLASTIC GmbH. This means that production planning does not have to be geared to an extruder’s maximum throughput, but rather is based on the maximum operating time of all extruders. The shortest set-up time, the batch size and the expected material loss yield the machine capacity (tonnes/year). This production volume and a high level of flexibility, paired with extreme ease of operation and maximum quality, determine in turn the company’s overall result.
Keeping quality consistent
Another essential building block of ICX® technology in this integrated approach is the achievable quality. By this, the compounder means not only the absolute quality figures for its products, but also quality on a consistent basis. Just as standardised technology makes efficient machine utilisation possible in the first place, it is also a key factor of consistent quality. Because only a standardised extruder geometry — a consistently uniform ratio of Do/Di and L/D parameters combined with uniform gravimetric dosing technology – ensures the required repeat accuracy. “We achieve this not only from batch to batch, but also when changing over from one line to another”, explains Stier. An example of the glass fibre content in a compound, measured by annealing residue, clearly demonstrates this, as shown in Graph 1. The customer’s specification for a 30 percent glass fibre reinforced PBT compound was 30 +/- 1.5 percent. The value actually determined for a 132 tonne large batch was 30 +/- 0.03 to 0.27 percent, just 1/10 the maximum possible tolerance. A similarly consistent pattern was obtained for 25 production batches of the same material, this time produced on different lines.
Using time wisely
Time is the next factor in the customer benefit formula covered by ICX® technology. “Thanks to our identical production concept, companies operating internationally in particular can be supplied with identical products from our locations in Germany, China and Brazil, provided the raw materials are available”, says Stier. This can lead to significant time savings, and thus tremendous cost savings, when validating materials. It should be noted however that the need for global yet local supply should ideally be communicated at the beginning of the collaboration, according to AKRO-PLASTIC. With its standardised model series, and resultant easier maintenance system, the compounder also saves a lot of time. Due to the reduced spare parts stocking this entails, an additional time advantage is gained in many cases. “The low number of spare parts doesn’t just save on cost, it also makes it easier for us to ensure that wealways have every part in stock”, notes Philipp Hennerici, Director of Purchasing, Investment & Services at AKRO-PLASTIC. “This impacts not only the production location in Germany, but also our foreign production sites, which we can immediately supply with replacement parts in case of urgency, without having to initiate lengthy ordering processes”.
“It is unwise to pay too much, but it’s worse to pay too little.”
The English author, art critic and social philosopher John Ruskin (1819–1900) stated this in his common law of business balance. Even if flexibility, quality and time are optimally balanced, price often plays the decisive role when it comes to a buying decision. “Our integrative approach allows us to operate in a cost-conscious manner in every area; for this reason, an attractive price is simply the sum of all efforts and represents the value of what customers expect for their added value”, Stier remarks.
Conclusion:
Stier concludes by stressing: “The product determines the machine; the machine does not determine the product”. AKRO-PLASTIC has made ICX® technology its working method and has implemented it systematically to the benefit of its customers.