Fluid injection technique (FIT)
Fluid injection technique (FIT) is used to manufacture components with thicker walls as well as components with hollow spaces. Either gas (GIT) or water (WIT)can be used as the fluid. The process variant recently tested for the first time at the Institute of Plastic Processing (IKV) Aachen combines WIT and GIT and expels the melt using a gas-vapour mixture. Another variant is the projectile injection technique (PIT), which will be explained below.
The following materials from AKRO-PLASTIC are suitable for the gas and water injection technique, depending on the application:
Cooling water pipes:
- AKROMID® A3 GM 20/10 4 WIT black (4529) = thin walls, safe process
Handles:
- AKROMID® A3 GF 30 1 GIT black (4619) = good surface finish, safe process
- AKROMID® A3 GF 15 1 GIT black (4620) = good surface finish, safe process
- AKROMID® B28 GF 50 1 GIT black (4732) = good surface finish, safe process
- AKROMID® B3 GF 30 1 GIT black (4598) = good surface finish, safe process
- AKROMID® B3 GF 30 1 GIT black (4599) extremely good surface finish
Pedals:
- AKROMID® A3 GF 30 1 GIT black (4619) = good surface finish, safe process
- AKROMID® B28 GF 50 1 GIT black (4732) = good surface finish, safe process
- AKROMID® B3 GF 30 1 GIT black (4598) = good surface finish, safe process
- AKROMID® B3 GF 30 1 GIT black (4599) = extremely good surface finish
- AKROMID® B3 ICF 15 (5026)= good surface finish, safe process
Fluid injection technique (FIT)
Fluid injection technique (FIT) is used to manufacture components with thicker walls as well as components with hollow spaces. Either gas (GIT) or water (WIT) can be used as the fluid. The process variant recently tested for the first time at the Institute of Plastic Processing (IKV) Aachen combines WIT and GIT and expels the melt using a gas-vapour mixture. Another variant is the projectile injection technique (PIT), which is explained below.
Irrespective of the chosen fluid, the following fill variants are used:
- Full shot method
These variants are characterised by a tendency toward better surface finishes and achieve better reproducibility, particularly with regard to dimensional accuracy. Nearly all our AKROMID®, AKROLOY® PA, AKROLEN®, and AKROTEK® types are suitable for the full shot method. The types identified by "GIT" or "WIT" in the nomenclature are extremely well suited. These compound variants, such as our AKROMID® A3 GF 30 1 GIT black (4619), have the advantage of a slightly reduced recrystallization temperature and the associated increased processing window.
- Melt backpressure method:
The component is completely filled and the melt is then forced back into the screw unit by means of fluid or a projectile.
- Secondary cavity method:
The component is completely filled and the melt is then forced into a secondary cavity by means of fluid or a projectile
- Backpressure method:
This method is used only with gas. Here gas is forced behind the component in a sealed mould. This presses the component onto the visually more attractive side of the mould, thereby avoiding sink marks.
- Short shot method / partial-fill method
- Inflation method:
The component is partially filled (generally 60-90%) and the melt is then inflated with fluid by means of an injector close to the sprue.
If the melt is displaced with a projectile as well as with the fluid, the process is called projectile injection technology (PIT). This can be combined with various filling methods as well as different fluids.
- Inflation method:
Water injection technique (WIT)
Water injection technique is a variant of fluid injection developed at the Institute of Plastics Processing (IKV), Aachen, Germany (link), in which water is used for production of hollow components. This technique is particularly useful for manufacturing rod-shaped components with diameters greater than 10 mm. The gas injection method is better suited for smaller diameters. The better cooling effect of the medium (water) is only apparent at diameters greater than 10 mm, and the cycle time is significantly reduced.
Materials have been developed by AKRO-PLASTIC specifically for this high technological standard in injection moulding. We identify these materials with the abbreviation "WIT" when special attention is given to the formation of extremely good surface finishes in the interior.
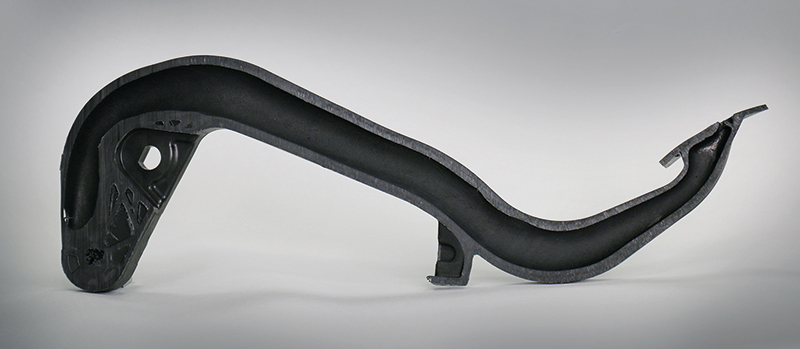
AKROMID® B3 GF 30 1 GIT black (4598)
AKROMID® B3 ICF 15 (5026)
Thus the Teklas company uses our AKROMID® A3 GM 20/10 4 WIT black (4529) to manufacture components used in the engine cooling circuit of various motor vehicles. The advantages of this material include the extremely easy processability of our AKROMID®, which has been specifically optimised for the water injection method. The material is used in the melt backpressure method and the secondary cavity method and is capable of forming walls up to 10% thinner compared with the competition. Thus it not only saves weight, but also ultimately saves our customers' money thanks to the reduced volume. Of course, our AKROMID® is able to meet the requirements of the most demanding OEMs in terms of cooling water resistance and dynamic strength. Please contact us should you have specific queries.
Projectile injection technique (PIT)
AKROMID® A3 GM 20/10 4 WIT black (4529) is also suitable for production of pipes with diameters greater than 30 mm. Projectile injection (PIT) was developed because physical properties dictate that the residual wall thickness of components increases as the diameter increases (rule of thumb: the residual wall thickness of the pipe is 1/8 – 1/10 of the outside diameter). With this technique the component is partially or completely filled, and the melt is then expelled from the cavity by means of a projectile made of plastic or metal. PIT is a suitable method particularly when the geometry, especially that of the cross section shape, is similar across the component. Slight changes in cross section can be handled using variable projectiles, but larger ones cannot. The advantage of PIT is that the thinnest residual wall thicknesses can be achieved with this method variant.
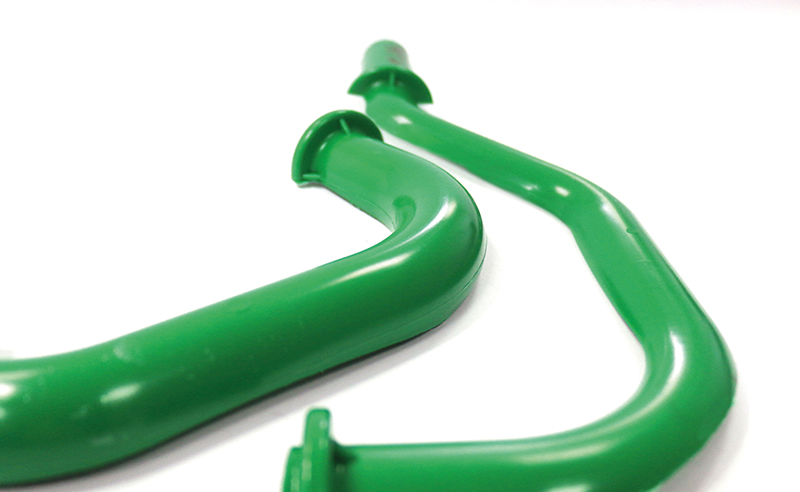
Gas injection technique (GIT)
The gas injection technique is oldest and most well-established FIT variant. GIT is used to form hollow bodies and as shrinkage compensation, and occasionally as a stopgap to save unfavourable mould designs. In this process nitrogen is typically used as an inert gas to prevent unnecessary oxidation of the plastic melts. More recent method variants from Maximator and PME use CO2 as the medium, thereby achieving further reductions in cycle time compared with the process using nitrogen.
The most important step, irrespective of the selected method, remains an appropriate process design for the component and, of course, the material used. We will be happy to assist you in selecting the right method and material for your products. Because with special methods, one thing is certain: the complexity of the process increases. Our materials are produced within such strict production tolerances that our AKROMID ®WIT and GIT types ensure a stable process. But it's not just the reproducibility that is greater than for most competitors; so, too, is our process window. A sophisticated polymer technology allows us to lower the recrystallisation point of the GIT and WIT types without negatively affecting the crystallinity. In the DSC curve shown here, the AKROMID® GIT variant demonstrates a recrystallisation temperature nearly 15°C lower than with identical recrystallisation enthalpy.
The result of this modification is beneficial for gas injection applications as well as standard injection moulding applications. The component cross section pictured here shows the area of a valve from AFT. The glass-fibre streaks in the area of the valve seat has reduced the service life of the seal and thus failed to meet the company's stringent requirements. The surface finish requirements were only met when AKROMID® A3 GF 15 1 GIT black (4620) was used.
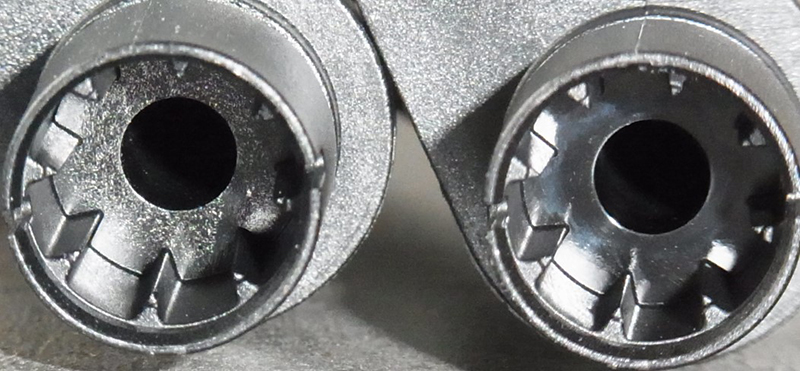
The following companies are involved with these methods:
GIT WIT plant technology
GIT WIT design and component testing
TiK, Technologie in Kunststoff
Do you also work in this area? Would you like to place a link to your page here? If so, please send us a short e-mail. Following verification, we will be happy to create a link to your website.
Please note that some of the methods mentioned here are patented in certain countries. Please address any queries regarding this to the plant manufacturers, who will be able to tell you which patents are covered with the purchase of the plant technology.
Disclaimer: All specifications and information given in this brochure are based on our current knowledge and experience. A legally binding promise of certain characteristics or suitability for a concrete individual case cannot be derived from this information. The information supplied here is not intended to release processors and users from the responsibility of carrying out their own tests and inspections in each concrete individual case. AKRO®,AKROMID®, AKROLEN®, AKROLOY®, AKROTEK® and ICX® are registered trademarks of the Feddersen Group.