Safety, apart from comfort, operability, level of intelligence and other indicators, is also becoming increasingly important in vehicle competition. That is why seat headrests of MPV models, especially luxury MPVs, seek to embody the best balance between safety and comfort. Let us take a close look at how AKRO-PLASTIC makes the seat headrest of a luxury MPV both safe and comfortable.
(Figure 1: Headrest)
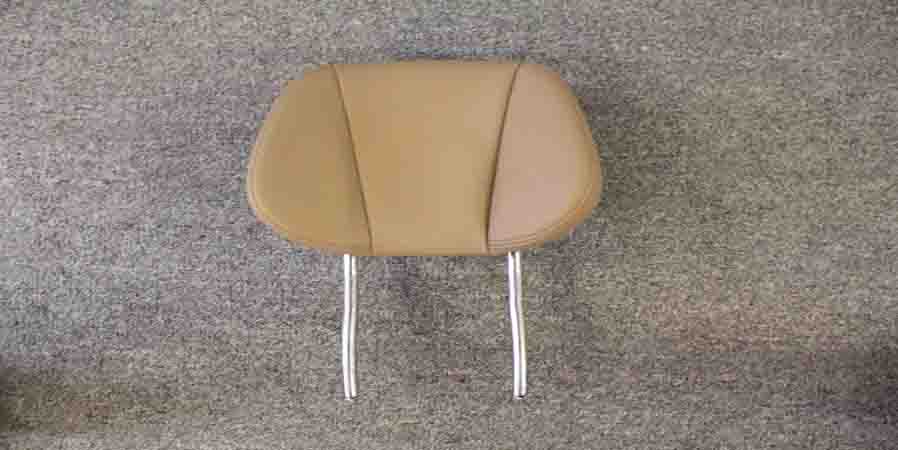
The manufacturer of this MPV, a well-known Sino-US joint venture automaker, and Yanfeng Adient Co., Ltd., the supplier of the seats, raised new expectations for the second-row VIP seat headrest at the very beginning of design concept of the new MPV model:
Comfort: This brand-new MPV model will adopt the concept seen in first-class aircraft cabins by pioneering the use of six-way adjustable aircraft headrests for its second-row seats, thus providing passengers with a comfortable experience.
Safety: In impact testing, the seat headrests both must provide support for the dummy's head, reduce neck displacement and protect the cervical spine. They must ensure the core components of the headrest do not break and cause secondary damage to the dummy.
Based on such expectations, the manufacturer put forward preliminary conceptualization for the material, including enough strength, durability under dry conditions (or dry environments), durability at low temperatures (or in low temperature environments), and extremely low friction noise (a property of NVH). The material and parts also had to satisfy requirements of low and high temperature testing and impact testing under the relevant harsh complex environments.
Facing such strict material requirements, AKRO-PLASTIC, the well-known German supplier of modified, engineering plastics, carried out a large number of model selection tests leveraging its expertise and engineering capability in the materials field and ultimately recommended its innovative material solution to this customer: the AKROMID® B3 Series PA 6 material.
The tenacity of PA 6 materials increases upon moisture absorption while with reduced strength. For this application, therefore, the solution needed to focus on the strength and toughness of components of the product in dry environments (in dry areas or during wintertime) and in low-temperature environments (like winters in northern regions). The AKROMID® B3 used at this time offers a notched impact strength of up to 34 KJ/m2 (ISO179/1eA) when the tensile modulus under dry conditions is 7500 MPa (ISO527). Its notched impact strength still maintains at 24 KJ/m2 (ISO179/1eA) at -30℃. Therefore, this material was sufficient to meet the requirements of this application.
The headrest has a quite complex structure comprised of core components, adjustment components and others. AKRO had overcome various technical challenges during upfront development through rigorous analysis and constant experimentation. This material was highly recognized by the said automobile manufacturer and Yanfeng Adient by successfully helping the new MPV model realize product upgrade, experience design and safety enhancement.
This headrest application is only one typical case of partnership between AKRO and Yanfeng Adient and the said Sino-US joint venture automaker. The PA 6 and PA 66 plastics from AKRO have obtained numerous certifications and are widely used in the automotive industry. Its carbon-fiber reinforced thermoplastics (CFRTP) are at the cutting edge of the plastics industry, boasting numerous mass production projects in the automotive industry.