轻量化高硬度的聚酰胺混合物
对于众多应用开发而言,减轻重量是一个非常重要的目标。例如,通过采用特殊的加工方法,一种新型改性混合物(聚酰胺+聚丙烯)的重量可降低30%。
塑料行业始终寻求各种方法以尽可能地减轻重量,因此,新的解决方案不断涌现。加入化学偶联的聚丙烯并吸水后,德国下齐森 AKRO-PLASTIC GmbH 新开发的聚酰胺混合物 (PA + PP)展现出了可媲美标准聚酰胺的强度。视具体的应用和增强程度,该混合物的密度可比标准聚酰胺低 7%-10%,并且流动性更好(见表 1)。为了进一步减轻零件重量,一种方法是用化学或物理发泡剂处理熔融物。
通过发泡进一步减重
注塑发泡是进一步减重的一种可行方法。在加压下将推进剂注入熔融物,在充模后或充模过程中使塑料发泡,从而减轻重量。而所谓的物理发泡则是通过复杂的工艺,在高压下将气体直接注入熔融物。专利问题的解决促进了这一工艺的推广。采用该技术通常可实现 6%-7% 的减重。而化学发泡则是通过色母粒将化学发泡剂加入塑料中。在加工过程中的熔融条件下,在塑化装置中形成推进剂。推进剂溶解于熔融物中,并在释压后的加工过程中将塑料发泡。这一色母粒解决方案不仅灵活性好,还有一个优势是可在色母粒配方中纳入其他成分。这为发泡带来了很多积极效果,还可根据使用的聚合物进一步优化加工方法。过去,用于工程塑料的化学发泡剂的选择很大程度上局限于放热发泡剂。但是,这些放能系统会导致冷却时间较长。此外,放热发泡剂的毒性分类也是问题重重。而吸热发泡剂(吸能系统)对机械性能又有可预见的负面影响,因此,对可市场化的吸热发泡剂的开发基本上停滞在 20 世纪 90 年代末期水平。过去,厚度小于 3 mm 的零件被认为不足以进行结构泡沫注塑成型。像 MuCell(供应商:美国马萨诸塞州威明顿市的 Trexel, Inc.)和 Cellmould(供应商:德国迈内尔茨哈根的 Wittmann Battenfeld GmbH & Co. KG)这样的物理发泡工艺之所以盛行,部分原因是由于没有合适的发泡剂色母粒系统
微孔泡沫的结构主要由塑料中的高含气量以及加工方法中使用的巨大压力差而产生。而相应的不利影响则有加工技术复杂、表面质量不佳、缺乏小批量加工的灵活性等。
堪称完美的色母粒
新的色母粒配方可有效降低这些不利影响。基础评估 [1] 以及本研究结果为开发新色母粒系统提供了理论基础。该系统可免除配方中的发泡剂造成破坏,同时也利于微孔泡沫的形成。泡沫结构的大小和数量很大程度上由成核速率 Nhet 决定。而Colton的研究(1)表明,成核速率可通过以下公式(2)求得:
其中C1 = 成核种浓度,f1 = 接触概率,ΔG*het= 成核自由能,Δp = 压力差,γ = 熔融物表面张力。
通过这一关系式可以得到生产具有细小泡孔结构的必要参数和影响因素。这些影响因素不只限于达到最大压力差(这一点是纯物理发泡工艺的必要条件)。现代发泡剂色母粒通过成核剂和添加剂,具有无尘和安全操作的优势,能够针对具体应用精确调整工艺。图 1 清楚地展示了最大成核速率的影响。开发用于轻质建筑的技术复合物时,不是要一味追求重量减轻,而是要在尽可能减重与尽可能保留技术塑料的机械性能之间达到平衡,比如需要:
· 保持硬度,
· 强度较好,
· 表面质量较好,
· 微孔泡沫结构。
在相互匹配的系统中,主要通过工艺来控制表面质量、机械性能(硬度和弯曲强度)和减重之间的平衡。使用张力测试条模具进行以下测试,该模具流径长,长宽比很高,很难获得表面质量良好且微孔泡沫分布均匀的模型制品。
然而,最终得到的制品却外观优异、重量明显减轻,还具有出色的机械性能。关于工艺控制,使用了两种不同的方法生产 4 mm 带侧翼测试条,原料使用由 AF-Color 生产的 20% 碳纤维加强的 (PA+PP) 混合物,再加入 3.5% 色母粒 AF-Complex® PE 990310 TM。表 2 比较了两种方法的结果,将加入了发泡剂,采用标准工艺生产的复合物设为 0 值。通过加入色母粒,最终复合物中碳纤维的比例随色母粒的用量增加而降低。
零件生产
足量注射:模具完全填满、压紧,不使用保压压力
,让机器即刻开始下一个计量冲程。此方法与不使用发泡剂的标准工艺相比,实现了 4% 的减重。机械参数基本保持一致。此方法的优点是生产的零件基本无翘曲,因为是由复合物自身来维持保压压力,在各个部位上同等有效。
此外,发泡剂提高了流动性,但在减重方面表现一般。密度降低主要集中在最热点。因此,视具体零件而定,冷却零件核心所需的制冷量降低,冷却时间即可缩短 10%。在零件表面质量方面,此方法得到的结果与标准工艺获得的零件同样出色。
欠注:模具几乎完全填满,但没有压紧熔融物。此方法也不使用保压压力,与 0 值相比实现了 13% 的减重。弹性模量降低了 15%,大致等于重量减轻的比率。不过弯曲模量仍高于 0 值。
这一结果可通过截面惯性矩来解释:硬度与外表面积的 x³ 具有特定关系。这导致加入了发泡剂的系统具有较低程度的收缩。另一方面,基质材料减少了 13% 也相应导致硬度降低。
总结
新的发泡剂可使得工程塑料减重,同时不会明显影响其性能。推荐使用相互匹配的系统,例如 (PA+PP) AKROMID® Lite 混合物和发泡剂色母粒 AF-Complex® PE 990310 TM。在本文描述的情形中,通过加入发泡剂,AKROMID® B3 ICF 20 1 Lite black (5296) 的密度降低了 13%。而通过混合物技术(PA+PP),又进一步减重了 8%。与聚酰胺 6 GF 30 相比,使用 AKRO-PLASTIC 生产的创新产品 ICF 碳纤维整体减重可能实现 30%,并且抗张强度和抗弯曲性更好。因此,此发泡复合物的密度显著低于水的密度(见标题附图),并且挠曲模量大于 12000 MPa(见图 2)。
参考文献:
1 Colton, J.S.:The nucleation of microcellular thermoplastic foam.Dissertation (MIT Thesis), 1985
2 Altstädt, V.; Mantey, A.:Thermoplast Schaumspritzgießen.Carl Hanser Verlag, Munich, Germany 2011
作者:
Thilo Stier 是德国下齐森 AKRO-PLASTIC GmbH 销售与创新部主管
Inno Gaul 博士是德国下齐森 AKRO-PLASTIC GmbH 的分公司 AF-COLOR 的研发部主管
表 1. 与标准聚酰胺相比,添加化学偶联的聚丙烯的聚酰胺具有重量较轻的优势
表 2. 标准工艺(加入/不加发泡剂)与欠注/足量注射工艺的比较
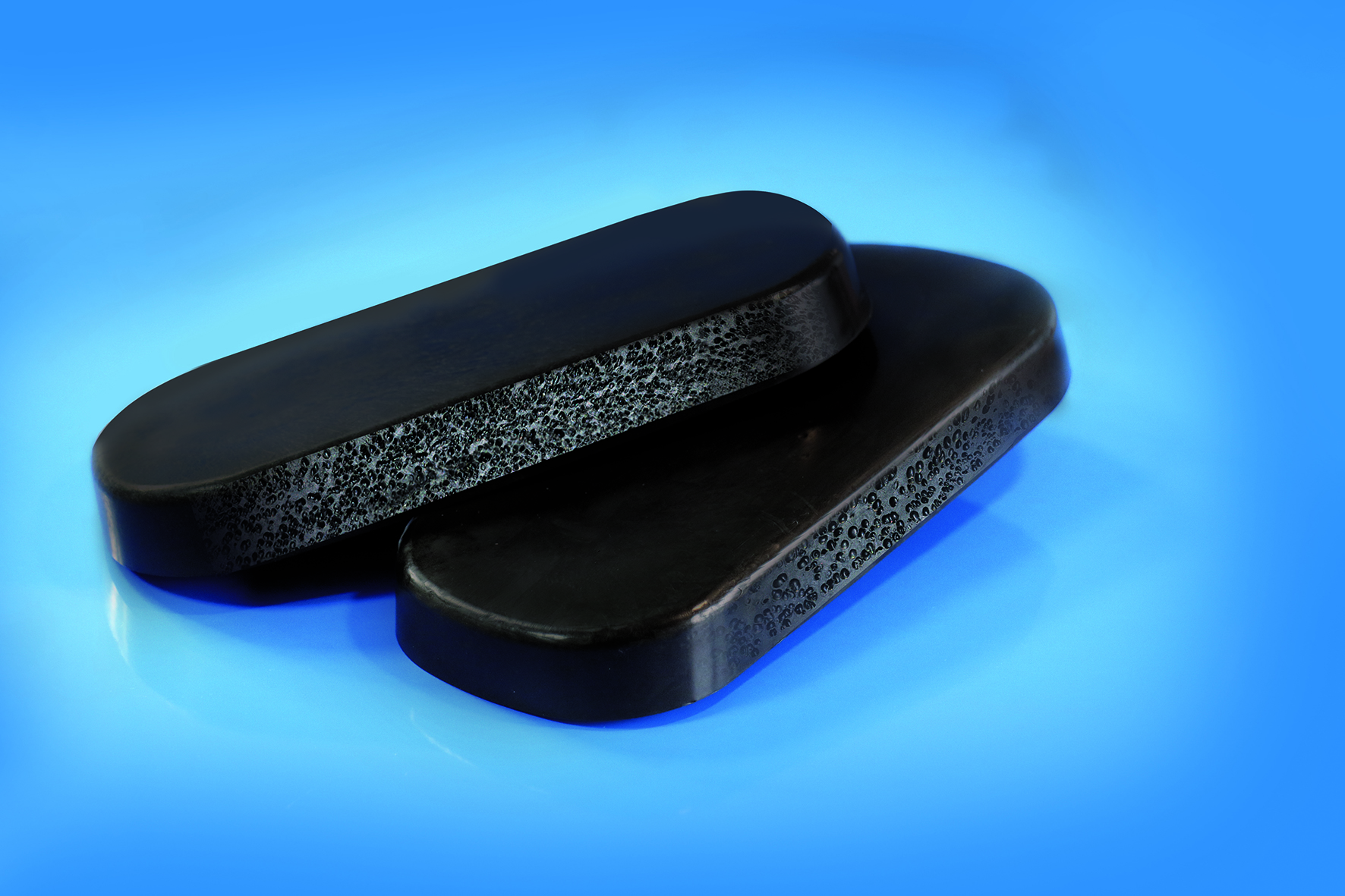
图 1:提高多样化成核的效果(上方零件:成核的,下方零件:未成核的)
图 2:使用 (PA+PP) 混合物 AKROMID® B3 ICF 20 1 L black (5296) 制造的张力测试条具有比水更小的密度