一直以来,工业产品的设计开发都停留在“发现问题,解决问题”的早期阶段,因此往往在项目前期投入了大量财力物力以及时间。然而经常在样品制作完成之后,才发现在产品设计上有很多棘手的问题。
此时,研发人员已经花费大量成本来开发模具、测试认证。而在发现问题后,我们不得不重新分析,更有甚者,前期投入的模具不得不报废。
那么,如何帮助研发人员在项目开发阶段期间就可以精准预估产品的结构是否合理,使产品的功能更符合设计需求,从而缩短项目开发时间,节约成本?随着工业需求的日新月异,这已经成为大家必须面对的问题。
作为一家提供从产品概念设计开发到最终工业实现所有阶段解决方案的提供商,AKRO-PLASTIC 安科罗的兄弟公司M.TEC - 前身隶属于德国亚琛大学旗下的IKV塑料研究所,目前正式开始在中国为用户提供方案服务。
从产品概念设计及可行性分析、结构设计、计算机仿真模拟、生产技术和风险分析评估等设计产品设计开发的各个方面,为用户提供全方位的支持。
1 产品概念设计
根据客户提供的产品要求,进行产品设计的可行性分析、风险分析,做出产品的概念设计以及初步的开发设计。
2 设计阶段
产品结构设计,基于结构及功能要求的材料选择,为客户提供优化的解决方案。
3 仿真分析
注塑工艺模拟,潜在失效模拟分析以及产品轻量化的仿真分析等。
4 验证阶段
产品模型,功能测试以及后续的测试试模等。
5 量产支持
注塑设备的选择、量产工艺优化、模具设计、功能认证以及产品生命周期管理。
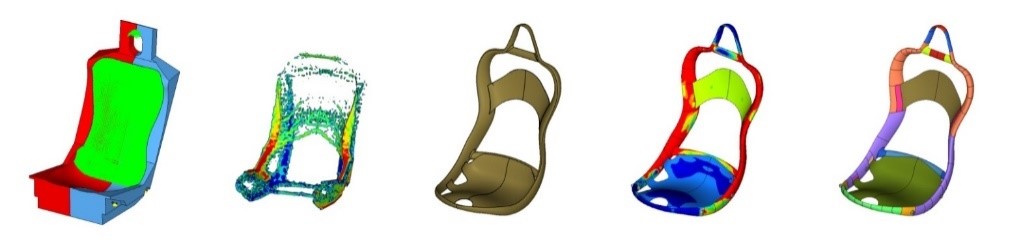
案例分析
计算机仿真模拟分析,贯穿于产品定义、设计加工、测试分析到工业化的整个过程。
参考以下案例,M.TEC如何通过计算机仿真技术实现产品的高效开发和设计:
a. 产品分析
1.明确产品失效方式,了解产品的使用及功能要求。
2.确认仿真分析工具—模流分析/有限元分析
b. 模流分析
1.明确产品工艺对材料及产品功能的影响
2.产品测试破裂纹和材料玻纤取向一致
c. 有限元分析
1.明确峰值应力应变的区域
2.峰值应力区域与产品破裂位置一致
d. 可行性优化方案
1.更换性能更好的材料
2.产品结构优化
3.模具结构优化(浇口位置变化,改变熔接线位置)
e. 样品通过
使用优化后的模型做极限测试条件分析,通过!
在本次案例中,我们可以发现优化模型的前提是在不增加零件重量的前提下,使用同样的材料,降低最大应力峰值。
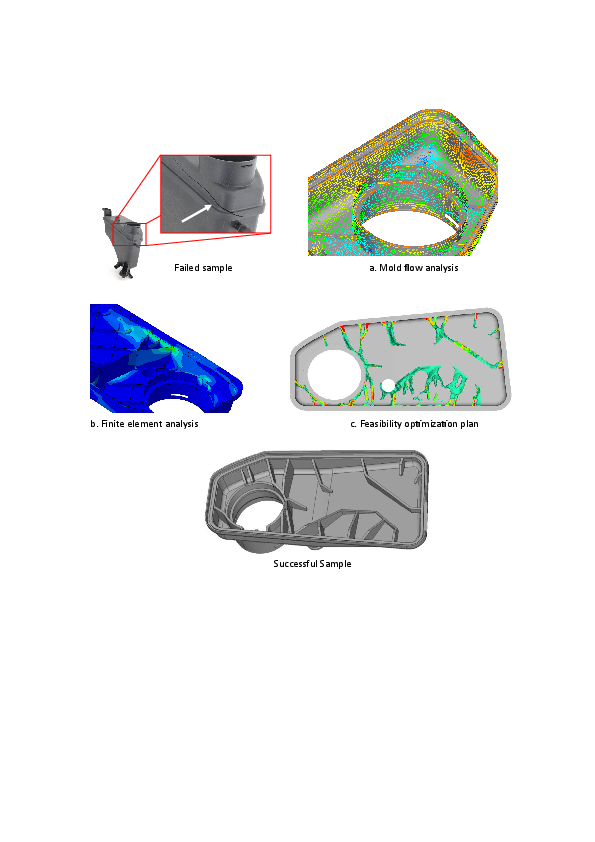
通过分析,我们找到了问题点并给出了优化方案。并通过计算机模拟验证优化方案,降低后续验证风险。实际改模后,产品测试顺利通过。
我们已经可以看到,中国工业设计的创新力量越来越令世界侧目。M.TEC 愿意与中国用户一起共同提升产品设计开发效率,用科技改变人类生活。
任何业务咨询需求及合作意向请联系K.D.F 中国座机 Tel: 86 21 64073666。
我们期待您的垂电!